Package sorting and distribution centres are the beating heart of the logistics industry. As eCommerce continues its meteoric rise, the demand for faster and more efficient package handling has reached new heights. Automated sortation systems provide the cutting-edge technology needed to keep up with ever-increasing consumer demand.
Automated sortation systems accelerate the speed, accuracy and overall efficiency of package handling operations. By employing advanced scanning, routing, and conveyor technologies, automated systems can process hundreds or even thousands of packages per hour. This represents a quantum leap compared to traditional manual sorting.
Companies like UPS, FedEx, and Amazon utilise vast networks of highly automated sortation centres to keep packages flowing smoothly through their distribution pipelines. The savings in time and labor costs are enormous.
How Do Automated Sortation Systems Work?
Modern automated sortation systems leverage a combination of technologies to optimise package routing and sequencing. Here are some of the key components:
- High-Speed Scanning: Packages are identified by barcodes, RFID tags or vision systems to determine their destination. High-speed cameras and sensors read these identifiers in milliseconds as packages rapidly move through the system.
- Destination Encoding: Based on the scanning data, a routing code is assigned to each package to designate its sort destination, such as a particular chute, outlet or loading dock.
- Conveyor Routing: Packages are transported through a network of conveyor belts, diverters, chutes and other mechanisms that route them based on their encoded destination. Sophisticated control systems synchronise the entire material handling process.
- Sequencing: Packages with the same destination are sorted in proper delivery order and grouped together on pallets or in containers. This sequencing step optimises loading and final-mile delivery.
Advanced software utilises machine learning and other AI technologies to optimise many aspects of automated sortation, such as traffic flow orchestration and anticipatory destination forecasting.
Key Benefits of Automated Sortation Systems
There are many reasons why automated sortation systems are becoming essential for high-volume distribution centres.
- Speed – Automated systems can process hundreds or thousands of packages per hour, far exceeding manual throughput. This allows fulfillment of tight delivery windows.
- Accuracy – Mistakes in manual sorting can lead to misrouted and delayed packages. Automated systems virtually eliminate errors through automated scanning and routing.
- Efficiency – With less manual labor needed, automated systems offer major cost savings while enabling 24/7 operation. Facility footprints can be reduced.
- Scalability – Modular automated systems can be easily expanded to handle seasonal peaks or business growth. Additional throughput can be added without linearly increasing labor.
- Tracking – Detailed data on package movement through the system provides insights for continuous optimisation. Inventory and asset tracking accuracy is improved.
- Ergonomics – Automated sorting eliminates most strenuous manual material handling to improve worker health, safety and satisfaction.
As package volumes continue rising, automated sortation enables logistics providers to keep pace without swelling labor costs. The systems pay for themselves through efficiency gains and superior accuracy compared to manual methods.
Implementing Automated Sortation Systems
Transitioning to automated sortation is a major project, but the return on investment can be significant. Here are some best practices for a successful implementation:
- Analyse current operations and future needs to right-size the system design. Seek vendor input.
- Integrate the new automation into existing warehouse management and inventory control systems for maximum visibility.
- Phase installations starting with the highest-volume processes or pain points. Take lessons learned into future phases.
- Train both IT and floor staff extensively on the new system. Emphasise software proficiency and mechanical maintenance.
- Start sorting less critical volumes first to shakedown the system, then ramp up. Closely monitor KPIs.
- Continually optimise the system as volumes increase over time. Add new capabilities via modular expansions.
Types of Automated Sortation Systems
There are several major types of automated sortation systems.
- Linear Sorters – Packages move in a straight line on a conveyor and are diverted to appropriate sorting destinations off the main line. This includes shoe sorters, tilt-tray sorters, cross-belt sorters, and bomb-bay sorters.
- Loop Sorters – Packages circulate continuously on a looped conveyor network and are diverted at their destination point to chutes or take-away conveyors. This includes tilt-tray and cross-belt loop sorters.
- Tilt-Tray Sorters – These have angled trays that tilt to divert packages to destination chutes/conveyors using gravity. Highly versatile.
- Bomb-Bay Sorters – Packages are temporarily held in a bay tilted in multiple directions for precise diversion targeting. Very high throughput potential.
Software and Controls
Central control software manages routing logic, communicates with scanners, actuates diverters, and monitors jams and errors. AI is used for traffic optimisation and anticipatory sorting. Sort schemes can be dynamically adjusted.
Facility Design Considerations
- Input and output conveyor lengths and positions impact efficiency. Simulation software models flow.
- Chutes and conveyors should be modular and expandable. Zoned power distribution.
- Ergonomic picking and loading areas with proper lighting and accessibility improve safety.
- Fire suppression and sufficient ventilation are critical around high-speed conveyors.
Maintenance Factors
- Preventative maintenance programs on conveyors, scanners, diverters and other components reduce downtime.
- Accessible design with spare parts inventory enables faster repairs when issues occur.
- Software analytics and sensors help predict component failures before they happen.
With strategic planning and deployment, automated sortation systems can provide logistics providers with an adaptable technological foundation for decades of growth. The capital investment pays back over the long term through substantial gains in workflow efficiency, accuracy and speed.
Empower your logistics with SmartlogitecX, fueled by WayZim Technologies. As leaders in Warehouse Automation for the Australian market, we’re dedicated to delivering efficiency and innovation right to your doorstep. SmartlogitecX’s approach is two-fold: globally informed, locally applied. Take the first step towards optimised operations by reaching out to our sales team for a solution that speaks directly to your needs.
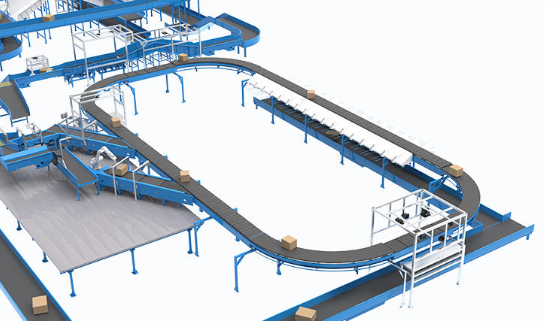