With the development of express parcel sorting, cross belt sorters have gradually replaced traditional manual sorters and become a mainstream means of large-scale sorting due to their advantages such as high efficiency, high accuracy, and low damage rate.
A cross belt sorter is mainly composed of components such as infeed modules, loop tracks, and discharge modules. To maximise the operating efficiency of the carrier units, starting from the infeed modules, the selection and design of the infeed method play a decisive role in whether the carrier units can accurately receive the parcels input by the infeed modules.
The current mainstream infeed methods include manual infeed, manual semi-automated infeed, and automated infeed.
The manual infeed method is to manually place a parcel’s label side up and convey the parcel to the sorting carrier.
Disadvantages: This method is limited to manual efficiency, and there is a possibility of misclassification.
This system is composed of an automated infeed platform and a manual infeed platform, and the operator performs infeed.
Advantages: This method has lower requirements for parcels from the front end. The parcels from the front end can be stacked, and abnormal parcels can be handled.
Disadvantages: Manual intervention can easily cause misclassification, and the efficiency depends on the proficiency of the operator.
This system is composed of an induction section, an acceleration section, and an infeed section. The infeed control computer controls the frequency converter and the drive motor to rotate the infeed belt. After being recognised by the intelligent camera, the parcel is accurately sent to the center of the sorting carrier.
Advantages: This system can achieve fully automated operation, and realise detection of all types of parcels and efficient and accurate infeed.
Configuration requirements: This system requires a complete configuration of diverting lines, 2D singulation equipment, merging lines, and pivot wheel sorters.
This method combines the advantages of semi-automated infeed and automated infeed. The combination of N (automated infeed) + 1 (semi-automated infeed) can be flexibly configured as needed.
Project Application
1. Introduction to the Actual Case
- Case: Main express distribution centre is in Huai’an, China.
- Delivery time: April 2022.
- Scale: About 130,000 m2.
- Configuration
This project is equipped with three double-layer double-zone small parcel cross belt sorters, and the peak processing capacity of one piece of sorting equipment can reach 50,000 pph in total.
The project adopts the parallel automated infeed mode, and provides double infeed areas to match the sorting efficiency of the main line. In addition, the following modes are planned according to the site space:
- ◆4+1 mode (connecting two pieces of 2D singulation equipment)
- ≡ Single line efficiency can reach 7,500 pph.
- ≡ The overall efficiency of a single infeed area can reach 15,000 pph.
- ◆6+1 mode (connecting three pieces of 2D singulation equipment)
- ≡ Single-line efficiency can reach 6,000 pph.
- ≡The overall efficiency of a single infeed area can reach 18,000 pph.
- Solution Performance
Compared with the processing efficiency of manual infeed (trained professional and skilled workers), which is 1000 to 1400 pph, this infeed solution improves the manual efficiency by more than 4 times. This solution perfectly matches the sorting efficiency of the cross belt sorter and meets the peak processing capacity of the main line.
In actual operation, the processing capacity of the three sorters in this project can reach 150,000 pph in total. The parallel design of the automated infeed in 4+1 mode or 6+1 mode can appropriately utilise the on-site space, and allow the efficient connection of the automated parcel sorting process by combining multiple automated infeed equipment with one piece of semi-automated infeed equipment between the 2D singulation equipment and the main line of the cross belt sorter.
Operating Track: 3D Bulk Singulation – 2D Singulation – Pivot Wheel Sorter – Infeed Station – Cross Belt Sorter[/caption]
At the project site, parcels are output into queues at certain distance through 2D singulation. After being eliminated by the pivot wheel sorter, the parcels are queued to enter the induction section, and then scanned and recognised by intelligent cameras.
Based on deep learning and spatial point cloud algorithms, the intelligent cameras can accurately recognise information such as quantities, positions, sizes, and types of parcels and perform data interaction with the control device, so that the conveying speed is fixed and matches the loop running speed, and the parcels are accurately inducted under control to the center of the belt of the fast-moving sorting carrier, to complete the infeed.
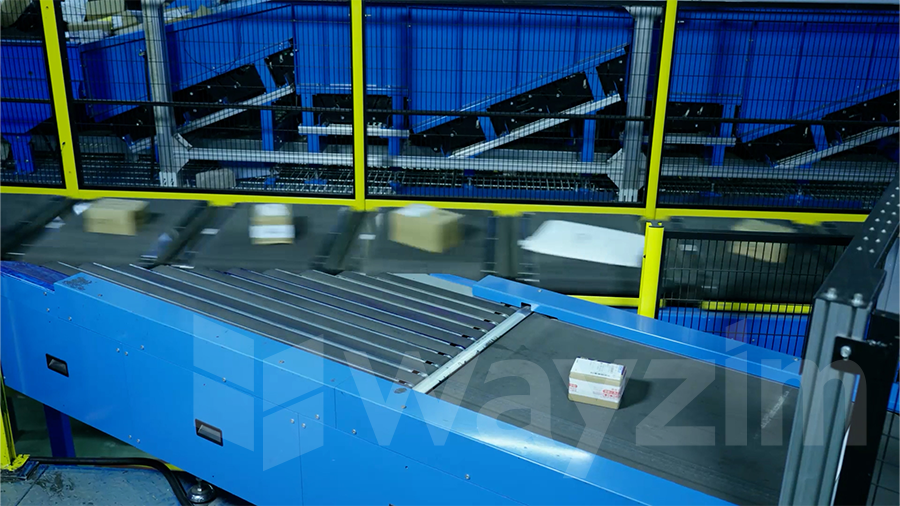
2. Solution Features
- Detection of all types of parcels
Wayzim’s automated infeed solution is based on RGB-D Intelligent Stereo Cameras. Combined with instance segmentation deep learning network and 3D spatial point cloud algorithm, the solution can efficiently and accurately recognise parcels and calculate their spatial position information, to realise detection on parcel information of all types in various complex application scenarios, including recognition of parcels’ type, size, and position information.
Therefore, the automated infeed is not limited by various factors such as parcel size, angle (flat or tilted), material (paper, plastic, etc.), and type (box, envelope, waterproof bag, woven bag, etc.). The recognition data provides a basis for determining intelligent alignment and path planning.
- Flexible matching and high adaptability
The combined use of semi-automated and automated infeed conveyors can effectively eliminate odd-shaped items and avoid misclassification and loss of parcels that may be caused by manual intervention through precise algorithms. This feature reduces dependence on personnel, improves infeed accuracy, and reduces training costs.The infeed conveyors in multiple modes can adapt to the processing capacity of the cross belt sorters based on different requirements for the infeed rates. - Intelligent sorting and path planning
Through data upload, the belt speed is controlled, and the corresponding carriers are allocated. Gapping is controlled during the infeed process, so that the parcels are separated from each other and run smoothly and efficiently to maximise the efficiency of cross-belt sorting.
Summary
As large distribution centres have higher requirements for the operating efficiency, accuracy, and stability of automated sorting systems, the application of automated infeed systems has become a trend. Based on the requirements in different scenarios, SmartLogitecX empowered by Wayzim can provide customers with a variety of modes of automated infeed, including parallel automated infeed and manipulator automated infeed.
SmartLogitecX gives full play to the advantages of product development and supporting algorithms for the intelligent logistics vision sensor and promotes industrial cost reduction and efficiency improvement through system integration solutions.